Manufacturing Benefits of Oil-Free Air Compressors
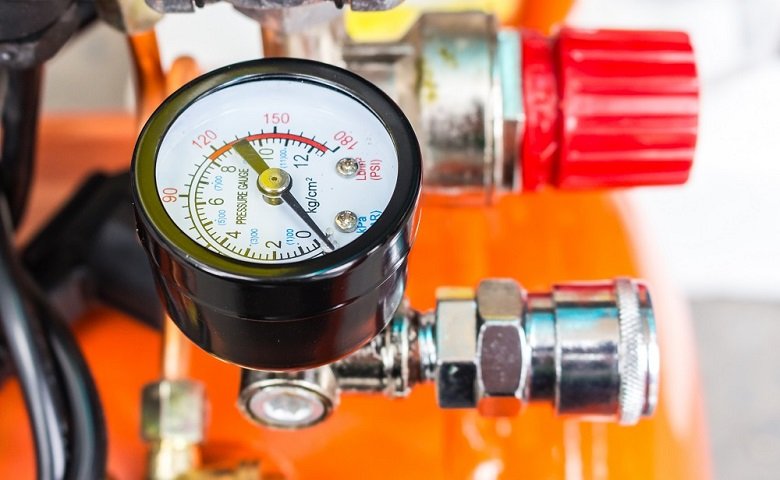
Manufacturers all around the country are challenged with lowering their operational expenses while keeping a stable, high-quality product with little to no environmental effect. Using an air compressor that produces ISO 8573-1 Class 0 certified oil-free air is one method to attain these goals in various sectors.
Oil free compressors are gaining popularity due to their capacity to decrease maintenance and energy costs, as well as their ability to reduce environmental footprint and the risk of product contamination.
Removes Contamination Risk
When compressed air comes into contact with an end product, contamination is always a possibility; the easiest approach to avoid this is to never bring oil into your airstream in the first place. Class 0 air helps producers to avoid contamination concerns such as post-filtration oil filter breakout, which would reduce product quality, raise the possibility of product recalls, and result in needless downtime. Contamination concerns may affect your brand’s reputation, bottom line, and, worse, your consumers’ health.
Oil-lubricated compressors will always leave a trace amount of oil in the air they generate. Pneumatic equipment and other essential assets that use compressed air can accumulate trace oil, raising maintenance and replacement expenses.
Reduces the impact on the environment
Following the relevant regulating authority requirements, this oil must be appropriately disposed of. Because oil is not used in the compression process, oil changes are only required every two to three years with oil-free compressors.
To protect the environment, substantial volumes of oil-contaminated condensate must be appropriately disposed of when running an oil-flooded compressor. Governing authorities often monitor and control the disposal of polluted condensate to guarantee compliance. Condensate from oil-free compressors may be readily disposed of or repurposed inside the facility for other use.
Lower Your Energy Bills
The more energy-efficient the compressor is, the more direct the machine’s influence on decreasing running costs will be. Because energy expenses account for 60-75 percent of an air compressor’s entire life-cycle expenditures, overall cost reductions from efficiency alone can amount to tens of thousands of dollars in life-cycle savings. To clean the compressed air produced by oil-flooded machinery, numerous oil filters and oil separators must be installed in the air route. Each of these factors will result in a pressure reduction across the filter, resulting in reduced air pressure downstream in the plant.
Lower Your Maintenance Costs
Operators can save money on maintenance by switching from an oil-flooded to an oil-free air compressor. There are fewer auxiliary air system components to maintain.
- Oil changes are spaced out over a longer period of time.
- The use of costly oil filters to clean compressed air is no longer necessary.
- Oily condensate handling is no longer necessary.
- The desiccant life of downstream air filters is extended.
- Downstream labor and outage-related expenses were reduced.
Now that you’ve learned about the advantages of oil-free compressors, At RVP, we welcome you to get the best air compressor life-cycle cost estimate to see how much you’re now spending and how much you may possibly save by switching to oil-free technology. RVP is one of the leading manufacturers and suppliers of Oil free compressors in China. Contact us for more information.
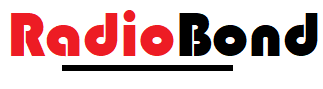